New Investment in Manufacturing
New Investment - Large Product Manufacturing
Click to Enlarge
Crane BS&U has completed a multi-million pound investment in the Viking Johnson factory at Hitchin that will strengthen its business model to deliver enhanced customer benefits in terms of ‘best in class’ service and products across a full range of pipe fittings. The investment has supported the creation of an entire linked value stream from the supply of raw materials through to the final manufacture of the products resulting in vastly improved lead times, product availability and plant flexibility.
The large diameter facility has also been re-organised into 3 dedicated lines, staff re-trained and the latest equipment installed. The new machinery, which includes a large ring bar bending machine, a vertical machining centre and flash butt welder, has increased both size and volume capacity and supports one piece flow through the factory.
Viking Johnson has recognised the growth in large diameter coupling demand across all 4 sectors - treatment, pipeline rehabilitation, new lay and desalination and the need to be able to react quickly to emergencies such as pipeline bursts. An emergency fastrack 24 hour service is available for a range of couplings and other pipe fittings such as flange adaptors, clamps and collars.
Can roll bars up to 75mm thick. This has eliminated 90% of segment welding, thereby reducing process time from 1 day to 100 minutes.
This Roundo can roll sleeves up to 300mm wide in comparison to the old machine that could only roll sleeves up to 180mm wide. MaxiFit items can now be manufactured in Line 1 increasing our capacity on Line 2.
Creates dimensionally stable rings of repeatable quality essential for the consistent compression of the annular gasket.
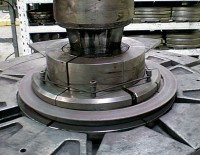
All VJ products are coated in Rilsan Nylon, a thermoplastic powder coating made from vegetable ricinus oil. It is environmentally friendly, resistant to corrosion and maintenance-free for product life expectancy.
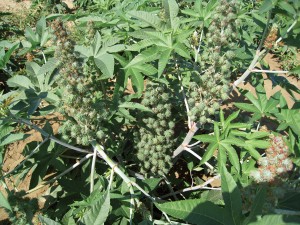
VJ utilises flash-butt welding for joining sleeves and rings together. It involves pressing 2 ends together and running a current between them, forming a seamless joint that is free of oxides. The benefit to customers is a first class coupling with a ‘solid state weld’ which will meet the required design life.
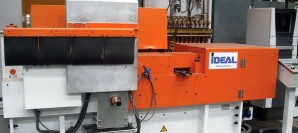
This vertical machine centre gives VJ the in-house milling and drilling capability of pipe fittings up to 2.8m wide. Previously, this process was subcontracted out and took 14 days.
For further information about our manufacturing plant improvements please download the following brochures available In English, French, German, Italian and Russian